Posted by:
Category:
Comments:
Post Date:
Quality Control vs Quality Assurance: What’s the Difference
It involves a proactive approach to quality, where the focus is on preventing defects and ensuring that the product meets the necessary standards. For many industries, compliance with regulations and standards is critical. Quality Control helps to ensure that products and services meet these regulations and standards, reducing the risk of fines and legal penalties. Quality control is the process by which services/products are measured and tested to ensure they are as uniform as possible and meet a standard.

"We just came off of two years of COVID, and ventilation is very key," he says. 2Life Communities facilities director Joe O'Toole lifts a panel to reveal a portion of the variable refrigerant flow system he's installed in a Newton, Mass., apartment building. It provides heating or cooling throughout the year based on demand, along with air filtration. The CDC's recent update to its ventilation guidelines recommends, among other things, that indoor air be exchanged at least five times every hour, which is well above that of the average household.
Key aspects of quality control
Earlier this fire season, authorities issued air quality warnings for Canada's capital Ottawa and financial capital Toronto. In the U.S., air quality alerts were issued for sections of the Midwest, the East Coast and the South, including New York, Washington and Chicago. For most consumer products, critical defects are not allowed, Quality assurance vs. Quality control and the AQL for major defects and minor defects are 2.5% and 4.0% respectively. Depending on the level you choose, the inspection might take only one inspector for one day, or up to 4 or 5 days of work. In this process, all the factors which are employed in the development of the product are taken into consideration for review.
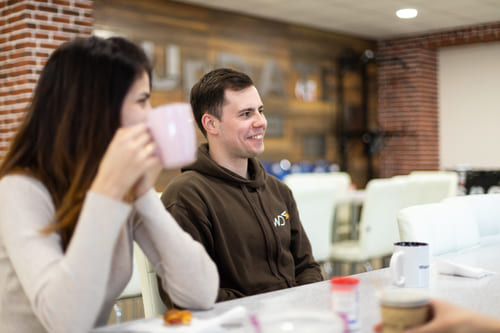
The primary goal is to prevent defects from reaching customers by identifying where and how they occur. A QA audit might even involve inspection techniques, like measuring a product straight from the manufacturing line. Like most types of inspections, quality control is focused on the tangible parts of a company’s offerings. When you need help with any step of the quality management process, Insight Quality Services is here to be your partner and adviser.
Definition of Quality Assurance
Even if your product is an intangible service, there will be room to implement QC and QA on the people, processes, and tools you use to provide it. The quality of a product is often impacted by deviations from target standards and by the high variability around target specifications. Effective quality control should be able to address both these issues. Quality control can help businesses in improving their products in the market along with brand recognition. It also helps in addressing liability concerns, planning and decision making, and meeting customer needs.
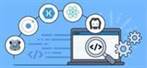
I.e. the activities of quality assurance come into play when the product is in the development process. However, the audit would play no part in accepting or rejecting that product, and it would instead be used to evaluate the process and controls involved. It’s best to https://www.globalcloudteam.com/ think of quality control as “under the jurisdiction” of quality assurance. While inspections and audits may use similar techniques to achieve their results, quality assurance is a big-picture process whose results influence how production and verification function.
Insight Quality Services
Inspectors therefore have the important task of detecting unsafe and defective products and rectifying the causes. If a visual check on all samples and a function/accuracy check on a few pieces is enough, it probably takes two or three man-days. Let’s say the 200 samples can be checked by one person in one day, so a third-party QC firm would quote you one man-day. You have no information about the factory, so you should adopt level II. In some cases, a buyer wants to make sure the factory ships the right products, in the right quantity, and with the right loading plan. Military Standard 105 was created by the US Department of Defense to control their procurements more efficiently.
Inspections during the loading and unloading of containers ensure that products are handled correctly during shipment. Inspectors monitor this process and ensure that the order is handled professionally. The process includes evaluating the condition of the container, verifying all shipping information, quantities, and checking the packaging.
The AQL (Acceptance Quality Limit)
” While this is reasonable for low-volume orders of goods, it becomes less and less possible as your order quantities increase. The more goods you order, the more time an inspection will take—and the more it will cost. When processes don’t work as they should, productivity suffers, and unexpected variations lead to product defects that compromise customer experience and a company’s bottom line.
- Most organizations have a quality control/assurance department that provides the set of standards to be followed for each product.
- The division referenced feedback it gathered from stakeholders and recommendations from an inclusive task force convened by the Colorado Energy Office, which will lead on running the program.
- The inspection that takes place during production itself is usually only carried out when working with a new producer.
- After that, it should plan the corrective actions which are to be undertaken to ensure the quality in the product.
- Don’t manually tie QA forms and QC data together—it’s a waste of time and effort.
- Nowadays people are becoming quality sensitive, and that is why they do not want to compromise with the product which is inferior regarding quality.
The program will also help the state meet its 2021 Greenhouse Gas Pollution Reduction Roadmap goal of reducing greenhouse gas emissions 50% statewide by 2030. Now, the air quality alert will only reach the orange category, and southwest and southeast Minnesota have been eliminated from the alert altogether. Reuters, the news and media division of Thomson Reuters, is the world’s largest multimedia news provider, reaching billions of people worldwide every day.
What Are the 4 Types of Quality Control?
Additionally, the entire state was under at least an orange-level alert. Canadian Prime Minister Justin Trudeau in June attributed the increase in the number of wildfires to climate change. Ellen Whitman, a research scientist with the Canadian Forest Service, said it is difficult to determine the impact of climate change on a single fire season. In much of that area, the number of new fires will taper off as autumn arrives. Large existing fires are expected to continue burning or smoldering, and new problematic fires can occur anywhere, the official said.
So check your local air quality index before cracking your windows, to be safe. The Minnesota Pollution Control Agency said this is the 16th air quality alert of the year, which breaks the previous record of 13 set in 2021. Thursday and Friday will mark the 42nd and 43rd alert days, which also breaks 2021's record of 42. What remains of the air quality alert will stay in effect until 11 p.m. Orange-level air quality is considered unhealthy for sensitive groups.
What Is Process Capability and Why It’s More Interesting Than It Sounds
Improve quality, reduce costs, and enhance efficiency with our expert insights. One solution to both dilemmas is releasing high-quality products that stand out from the pack and encouraging consumers to buy them. After all, most intelligent shoppers don’t mind paying a little extra for a premium product.